分享:机器学习辅助2000 MPa级弹簧钢成分和热处理工艺开发
杨累1,2, 赵帆,1,2,3, 姜磊1,2, 谢建新1,2,4
1.
2.
3.
4.
通过收集弹簧钢及其他典型淬火+回火型钢铁材料的文献数据,采用面向性能的机器学习设计系统(MLDS)结合实验优化,实现了具备超高强度和良好塑性的新型弹簧钢化学成分及热处理工艺参数的快速设计。所开发的2种新型弹簧钢的抗拉强度分别为2183.5和2193.0 MPa、屈服强度分别为1923.0和2024.5 MPa、断后伸长率分别为10.5%和9.7%、断面收缩率分别为42.4%和41.5%。新型弹簧钢的强化方式以晶界强化和位错强化为主,细小的晶粒尺寸和适量的奥氏体使得弹簧钢在具备超高强度的同时保持良好的塑性。与现有同等强度级别的超高强度钢相比,新型弹簧钢具有显著的成本优势和工艺优势。
关键词:
作为重要的机械基础零件,弹簧在服役时受到周期性弯曲、冲击、扭转等交变式载荷,这对弹簧钢的各项性能提出了较高要求,如强度、塑韧性、疲劳性能、抗弹减性能等。高速列车转向架弹簧用钢是弹簧材料中性能要求较高的一类钢种,转向架是列车实现高速运行的关键部件,其通过弹簧与车体和轮对相连,因而弹簧钢的力学性能对列车服役的安全性和舒适性产生重要影响。另一方面,随着弹簧钢力学性能的提高,有利于实现列车轻量化,减少线路损害、动力消耗、系统负荷和周边噪音。根据中国铁路总公司于2013年下发的《铁路客车转向架用钢制螺旋弹簧技术要求》,目前高速铁路转向架弹簧用钢的牌号为60Si2CrVAT,其同时也是国家标准GB/T1222—2016《弹簧钢》中强度级别最高的钢种,抗拉强度(Rm)、屈服强度(Rp0.2)、断后伸长率(A)和断面收缩率(Z)分别要求达到1860 MPa、1665 MPa、9%和30%。2019年我国发布的《交通强国建设纲要》将时速400 km/h以上的高铁和高速重载货运列车作为下一步研究开发的重点任务,这对弹簧钢的力学性能提出了更高要求,开发抗拉强度在2000 MPa以上且具有良好塑韧性的新一代超高强度弹簧钢受到了科研人员和工业界的关注。
改变合金成分[1~3]和热处理工艺[4~10]是调控弹簧钢力学性能的2个主要手段。然而,钢铁材料合金元素种类多、影响机理复杂,通过传统的“试错”方法难以快速开发出满足各项性能需求的合金成分。弹簧钢的常规热处理方式是淬火+回火,随着回火温度的降低,可有效提高材料的强度,但不可避免地会降低材料的塑韧性。强度和塑性的矛盾关系也是高强度材料开发所面临的共性问题。并且,随着合金成分的变化,最优的热处理工艺参数也会发生改变,进一步增大了材料开发的难度。近年来,随着材料基因工程的快速发展,机器学习在各类材料的设计和预测方面取得了诸多实质性进展,大大缩短了高性能新材料的研发周期[11,12],如传统合金材料[13~15]、非晶材料[16,17]、钙钛矿光伏材料[18,19]等,有望成为破解钢铁材料这一复杂合金成分-工艺-性能关系的有力工具。
本工作收集了弹簧钢及其他典型淬火+回火型钢种的化学成分、热处理工艺参数和力学性能的文献数据作为样本数据,通过机器学习方法实现具有高强度和良好塑性弹簧钢的成分和热处理工艺参数逆向设计,结合热处理实验优化获得了具有良好塑性的超高强度弹簧钢,有望为超高强度钢铁材料的研发提供新视野。
1 实验方法
1.1 样本数据
弹簧钢的化学成分涉及C、Si、Mn、Cr、V等多种合金元素,合金元素在钢中可以起到细化晶粒、改善淬透性、提高回火稳定性等作用,从而提高钢的综合性能,但不同合金元素对钢的组织和性能产生的影响大不相同。除了化学成分,影响弹簧钢组织和性能的另一重要因素是淬火+回火热处理工艺。因此,收集弹簧钢的化学成分(C、Si、Mn、Cr、Ni、Mo、V、Nb)、淬火温度(TQ)、淬火时间(tQ)、回火温度(TT)、回火时间(tT)、Rm、A作为样本数据。同时,为了扩大数据寻优空间和提高机器学习模型泛化能力,在收集弹簧钢数据的同时,也收集了部分轴承钢、模具钢、齿轮钢等其他采用淬火+回火热处理工艺的典型钢种数据,最终收集到样本数据共588组,其中弹簧钢351组,其他钢种237组。
1.2 机器学习设计系统
采用本课题组开发的机器学习设计系统(MLDS)[13],其原理如图1所示。该系统主要包括2个神经元网络模块,分别是性能预测成分的P2C神经元网络模型和成分预测性能的C2P神经元网络模型,2个模型的隐含层均为2层,具体结构如图2所示。C2P模型将化学成分和热处理工艺参数这12个参数作为输入,抗拉强度和断后伸长率作为输出,是一种降维拟合过程,可靠性较高。而P2C模型正好相反,是一种升维拟合的过程,其可靠性较差。该系统通过上述2个神经元网络模型的对抗,实现面向性能的成分和工艺参数高效设计。首先,将目标性能(抗拉强度(2050 ± 50) MPa,断后伸长率10.5% ± 1.5%)输入已训练好的P2C模型,得到目标性能对应的预测成分和热处理工艺。然后,将预测成分和热处理工艺输入已训练好的C2P模型得到预测性能,将预测性能与目标性能之间的误差与设定误差进行对比,如果误差过大,则使用P2C模型重新预测化学成分,如果误差符合要求,则选用该设计成分和热处理工艺。在此过程中,C2P模型筛选P2C模型的预测结果,不起到优化P2C模型的作用。
图1
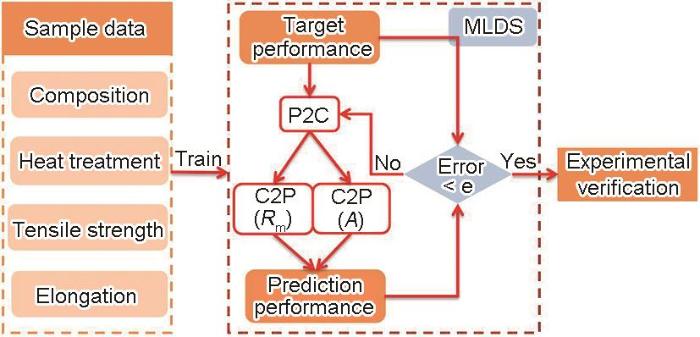
图1 机器学习设计系统(MLDS)原理图
Fig.1 Schematic of machine learning design system (MLDS) (Rm—tensile strength, A—elongation after fracture)
图2

图2 神经元网络结构图
Fig.2 Structure diagrams of neuron networks (tT—tempering time)
(a) P2C model (b) C2P model
采用split函数按4∶1的比例将样本数据随机划分为训练集和测试集。在训练集上进行模型超参数的优化(测试集不参与超参数优化),评价标准为实际值与模型训练后预测值的绝对百分比误差(MAPE),计算公式如下:
式中,n为数据个数,t为每组数据的序号,P为机器学习预测的性能,Q为文献给出的性能。具体优化方法是:采用KFold函数将训练集划分为5份,进行五折交叉验证,此划分过程随机进行50次,选用50次五折交叉验证的MAPE平均值最小的超参数作为神经元网络模型的最终超参数。C2P模型和P2C模型优化后的节点结构分别为12-58-20-2和2-5-10-12,2个模型优化后的学习率均为0.001,最大迭代次数均为15000,其他参数保持默认值。随后,采用优化的超参数在整个训练集上进行模型的训练,获得最终预测模型。
1.3 实验方法
选取MLDS设计的2种典型合金成分进行实验研究,实验用钢采用真空感应熔炼获得,铸锭质量为25 kg。通过轧制获得直径为24 mm的圆棒,开轧温度约为1150℃,终轧温度约为850℃。随后,采用MLDS设计的淬火+回火工艺进行热处理,测试钢的力学性能,验证机器学习结果。最后,采用实验研究热处理工艺参数对力学性能和显微组织的影响规律,优化实验用钢热处理工艺。热处理试样为直径12 mm、长85 mm的圆棒试样,标距段长度为25 mm,标距段直径为5 mm。热处理采用KSL-1200箱式电阻炉,力学性能测试采用CMT 5205拉伸试验机。采用Regulus 8100扫描电子显微镜(SEM)、Talos F200X透射电子显微镜(TEM)、Smartlab X射线衍射仪(XRD)等设备分析显微组织中的物相、界面以及微观结构。SEM试样采用4% (体积分数)硝酸酒精腐蚀,TEM试样采用机械减薄+氩离子减薄或碳萃取复型的方式制备,XRD试样为抛光态,电子背散衍射(EBSD)试样采用15% (体积分数)高氯酸酒精溶液进行电解抛光,EBSD分析时的扫描步长为0.1 μm。
2 实验结果
2.1 机器学习模型建立
C2P模型的训练结果如图3所示。图中的Pearson相关系数R是用来衡量X轴和Y轴之间相关性的一个参数,其取值范围在[-1, +1]之间,绝对值越大,表示2个变量之间相关性越大。图中黑色实线表明实际性能与预测性能一致,点越靠近黑色实线,模型的预测准确度就越高。可见,C2P模型在性能预测上具有良好的可靠性,但如果仅依靠C2P模型通过穷举来进行合金成分的设计,设计效率很低。在本工作中,MLDS将P2C模型与C2P模型结合起来,从而实现面向目标性能的化学成分和热处理工艺参数逆向设计。
图3

图3 抗拉强度和断后伸长率的C2P模型训练结果
Fig.3 Training results of the C2P model (R—Pearson correlation coefficient)
(a) tensile strength (b) elongation after fracture
2.2 化学成分和热处理工艺预测
以抗拉强度(2050 ± 50) MPa、断后伸长率10.5% ± 1.5%作为目标性能,分别输入P2C模型和MLDS预测弹簧钢的化学成分和热处理工艺参数,选取Si、Mn、Cr和Mo的元素含量以及热处理工艺参数TQ、tQ、TT和tT进行分析,结果如图4所示。可以看出,由MLDS设计得到的化学成分含量和热处理工艺参数相对集中,波动起伏较小。Si、Mn、Cr和Mo元素含量的波动方差由P2C模型的0.27、0.16、0.32和0.09分别降低至MLDS的0.05、0.05、0.10和0.04,热处理工艺参数TQ、tQ、TT和tT的波动方差由P2C模型的17.73、4.04、8.49和5.80分别降低至MLDS的5.86、0.62、3.97和2.21,由此可见,MLDS在化学成分和热处理工艺参数预测时具有更好的稳定性。
图4
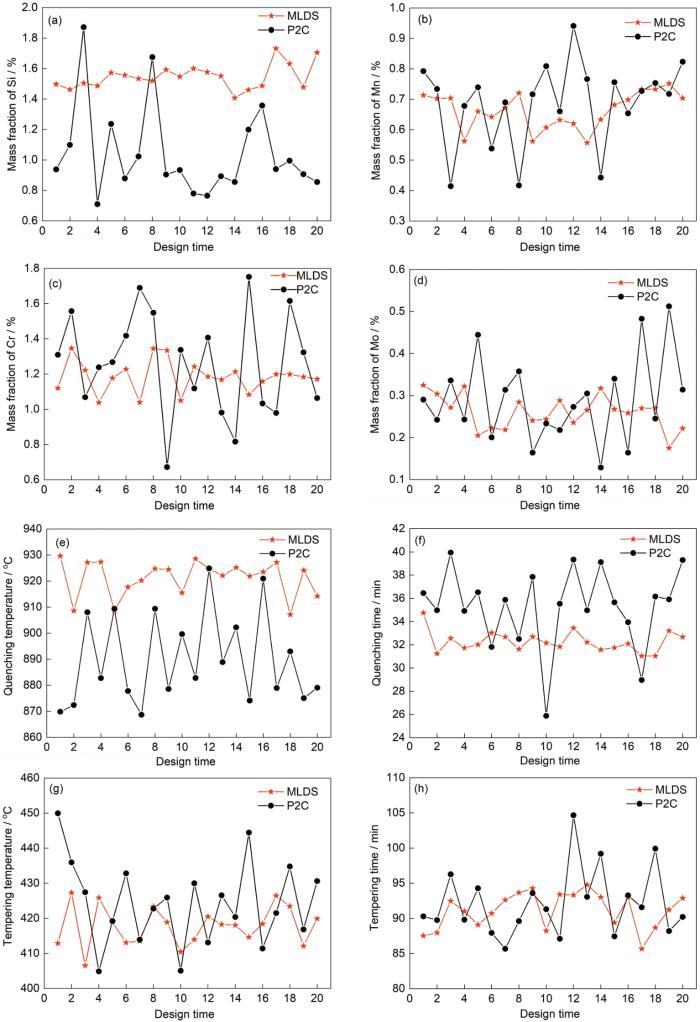
图4 MLDS和P2C模型所设计元素含量和热处理工艺参数的波动分析
Fig.4 Fluctuation analyses of design results by the MLDS and the P2C model
(a) Si content (b) Mn content (c) Cr content (d) Mo content
(e) quenching temperature (f) quenching time (g) tempering temperature (h) tempering time
图5a为抗拉强度和伸长率的样本数据和MLDS得到的40组预测数据,图5b为40组预测数据区域的放大图。选择了强塑积最高(图5b中的1#)和强度最高(图5b中的2#)的2组预测数据进行实验验证和后续研究。实验验证结果如表1所示。可见,1#钢的Nb含量较高,而2#钢的V含量较高。并且,与常见弹簧钢化学成分相比,设计成分中出现了少量的Mo元素和Ni元素,这可能是机器学习系统从其他钢种的数据中学到的“经验”。另外,设计成分的C含量处于中碳钢的范围内,有利于降低钢的表面脱碳敏感性;Si含量较高,有利于提高材料的抗弹减性能。抗拉强度和伸长率的预测和实验结果表明,MLDS具有良好的预测准确性。
图5

图5 抗拉强度和伸长率的样本数据和MLDS设计结果
Fig.5 Tensile strength and elongation of sample data and design results obtained by the MLDS
(a) all data (b) magnification of design results area for rectangle zone in Fig.5a
表1 MLDS预测结果和实验验证结果的比较
Table 1
Steel | Chemical composition (mass fraction / %) | Heat treatment parameter | Mechanical property | |||||||||||||
---|---|---|---|---|---|---|---|---|---|---|---|---|---|---|---|---|
C | Si | Mn | Cr | Ni | Mo | V | Nb | TQ | tQ | TT | tT | Rm | A | Rp0.2 | Z | |
oC | min | oC | min | MPa | % | MPa | % | |||||||||
1# predicted | 0.50 | 1.63 | 0.73 | 1.20 | 0.21 | 0.27 | 0.14 | 0.020 | 907 | 31 | 423 | 89 | 2075 | 12.0 | - | - |
1# actual | 0.55 | 1.76 | 0.70 | 1.10 | 0.21 | 0.20 | 0.14 | 0.016 | 910 | 30 | 420 | 90 | 2046 | 11.9 | 1644 | 38.0 |
2# predicted | 0.57 | 1.70 | 0.70 | 1.17 | 0.18 | 0.22 | 0.34 | 0.010 | 914 | 33 | 420 | 93 | 2096 | 10.9 | - | - |
2# actual | 0.54 | 1.75 | 0.64 | 1.18 | 0.20 | 0.20 | 0.37 | 0.003 | 910 | 30 | 420 | 90 | 2044 | 10.0 | 1695 | 33.9 |
2.3 热处理工艺优化
综上,设计成分和热处理工艺参数可获得设计目标要求的抗拉强度和伸长率,然而屈强比仅达到0.8左右,还有一定的提高空间。对于弹簧钢来讲,较高的屈服强度意味着较高的弹性极限,有必要通过热处理工艺参数优化提高设计钢种的屈服强度。因此,在MLDS设计的热处理工艺参数基础上,开展热处理工艺参数对弹簧钢显微组织和力学性能影响的实验研究。
2.3.1 淬火温度
控制淬火保温时间为30 min,回火温度为420℃,回火时间为90 min,研究淬火温度(870、890、910、930和950℃)对弹簧钢组织和性能的影响。1#钢和2#钢在不同温度淬火后(未回火)的XRD谱如图6所示。在不同淬火温度下,钢中的残余奥氏体含量均较低,体积分数在2%以下。不同温度淬火后(未回火)试样显微组织的SEM像如图7所示。随淬火温度升高,马氏体板条有所粗化,但碳化物回溶更加充分。
图6

图6 1#钢和2#钢在不同温度淬火后的XRD谱
Fig.6 XRD spectra of samples after quenching at different temperatures
(a) 1# steel (b) 2# steel
图7
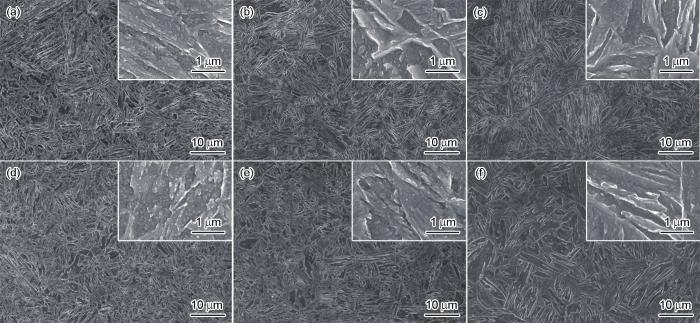
图7 1#钢和2#钢在不同温度淬火后显微组织的SEM像
Fig.7 SEM images of 1# steel (a-c) and 2# steel (d-f) after quenching at 870oC (a, d), 910oC (b, e), and 950oC (c, f) (Insets show the enlarged images)
图8为1#钢和2#钢在不同温度淬火并回火后的力学性能测试结果。可见,随淬火温度升高,抗拉和屈服强度变化均不显著,其中抗拉强度略有上升趋势。1#和2#钢的抗拉强度差别很小,均处于1980~2050 MPa范围内;2#钢的屈服强度高于1#钢,分别约为1700和1620 MPa。在910℃保温淬火时,塑性指标有所下降,其他淬火温度下塑性差别不大。由图7可以看出,淬火温度升高至910℃时,碳化物的回溶程度显著提高,但由于此时温度较低,元素均匀程度较差,导致塑性有所降低,为了碳化物更充分的回溶和合金元素更均匀的分布,选择950℃作为淬火温度,进行后续研究。另外,图8c给出了采用C2P模型预测的不同淬火温度时的力学性能。可见,预测结果与实测结果的变化趋势基本一致,抗拉强度的预测误差绝对值在18.6~82.3 MPa之间,断后伸长率的预测误差绝对值在0.3%~2.0%之间。
图8
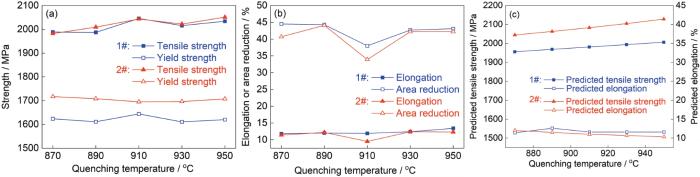
图8 淬火温度对力学性能的影响
Fig.8 Effects of quenching temperature on mechanical properties
(a) tensile and yield strengths (b) elongation after fracture and reduction in area (c) prediction results of the C2P model
2.3.2 淬火时间
控制淬火温度为950℃,回火温度为420℃、回火时间为90 min,研究淬火保温时间(15、30、45和60 min)对弹簧钢力学性能的影响,如图9所示。可见,随淬火保温时间延长,抗拉强度变化不显著。随着淬火保温时间由15 min延长至30 min,碳化物的回溶以及元素的扩散更加充分,使得1#和2#钢的屈服强度略有升高,塑性也有所改善;但随着淬火保温时间进一步延长,显微组织会发生粗化,使1#和2#钢的屈服强度和塑性均下降。选择30 min作为淬火保温时间,进行后续研究。另外,图9c给出了采用C2P模型预测的不同淬火保温时间时的力学性能。可见,预测结果与实测结果的变化趋势基本一致,抗拉强度的预测误差绝对值在2.3~117.4 MPa之间,断后伸长率的预测误差绝对值在0~1.8%之间。
图9

图9 淬火保温时间对力学性能的影响
Fig.9 Effects of holding time before quenching on mechanical properties
(a) tensile and yield strengths (b) elongation after fracture and reduction in area (c) prediction results of the C2P model
2.3.3 回火温度
控制淬火温度为950℃,淬火保温时间为30 min,回火时间为90 min,研究回火温度(380、400、420、440和460℃)对弹簧钢组织和性能的影响。1#钢和2#钢在不同温度回火后的XRD谱如图10所示。随回火温度升高,钢中的奥氏体含量降低;回火温度为440和460℃时,奥氏体含量很低,难以测出,这是因为在较高回火温度下,淬火时产生的残余奥氏体发生了分解;当回火温度为380、400和420℃时,钢中含有6%~8% (体积分数)的奥氏体,与淬火后相比,奥氏体含量明显增大,这说明在回火过程中又产生了一定量的逆变奥氏体。
图10
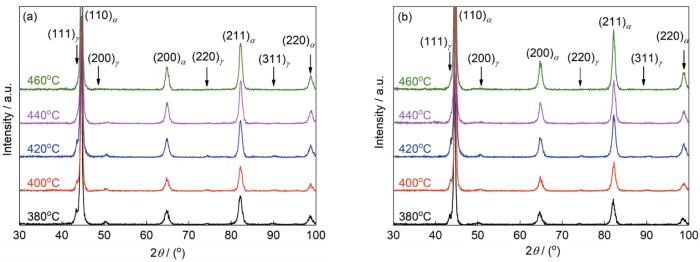
图10 1#钢和2#钢在不同温度回火后试样的XRD谱
Fig.10 XRD spectra of samples after tempering at different temperatures
(a) 1# steel (b) 2# steel
1#钢和2#钢在不同温度回火后显微组织的SEM像和TEM像分别如图11和12所示。回火后的显微组织主要为回火屈氏体,随回火温度升高,马氏体发生回复,马氏体板条粗化,碳化物的析出量增大,使得位错密度降低。
图11
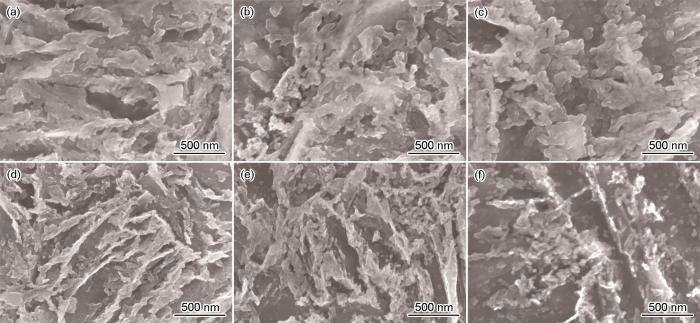
图11 1#钢和2#钢在不同温度回火后显微组织的SEM像
Fig.11 SEM images of 1# steel (a-c) and 2# steel (d-f) after tempering at 380oC (a, d), 420oC (b, e), and 460oC (c, f)
图12
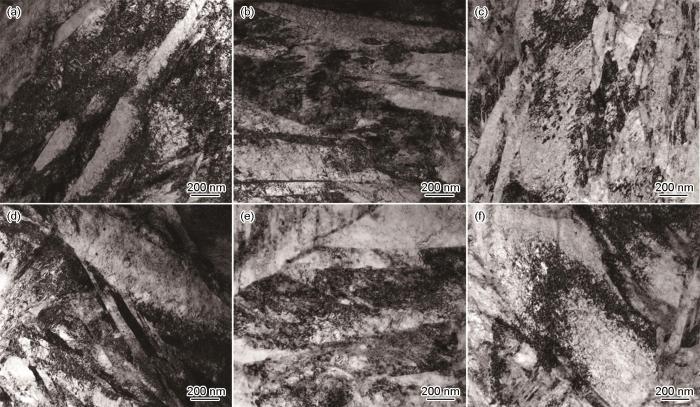
图12 1#钢和2#钢在不同温度回火后显微组织的TEM像
Fig.12 TEM images of 1# steel (a-c) and 2# steel (d-f) after tempering at 380oC (a, d), 420oC (b, e), and 460oC (c, f)
回火温度对力学性能的影响如图13所示。可见,回火温度对材料的强度有着显著影响,随回火温度降低,材料的抗拉和屈服强度逐渐升高,当回火温度降低至400℃时,1#和2#钢的抗拉强度达到2100 MPa以上,屈服强度达到1850 MPa以上,材料的屈强比达到0.9左右。并且有趣的是,随着强度的显著提高,材料的塑性并没有明显降低,断后伸长率维持在10%~14%,断面收缩率维持在35%~45%。选择380℃作为回火温度,进行后续研究。另外,图13c给出了采用C2P模型预测的不同回火温度时的力学性能。可见,预测结果和实测结果的变化趋势基本一致,抗拉强度的预测误差绝对值在2.3~124.0 MPa之间,断后伸长率的预测误差绝对值在0.3%~2.0%之间。
图13
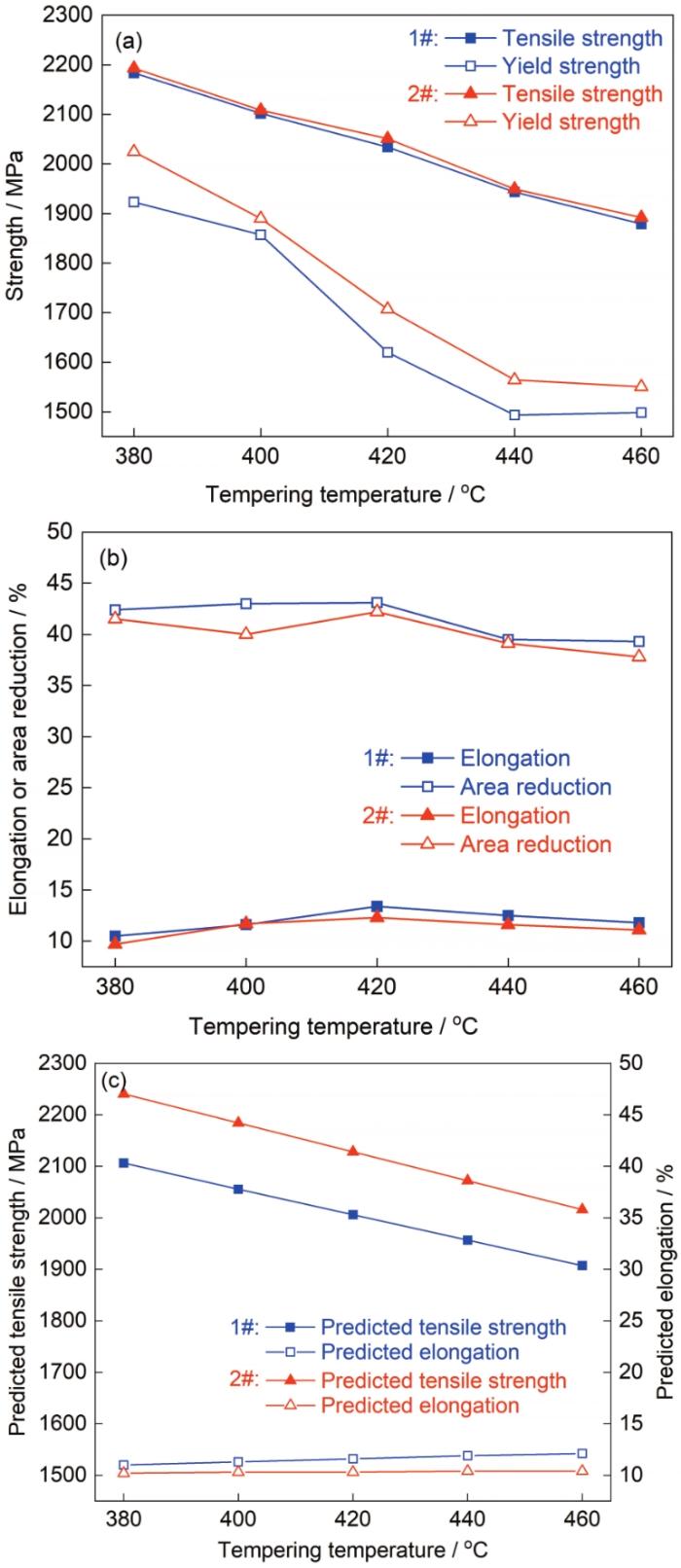
图13 回火温度对力学性能的影响
Fig.13 Effects of tempering temperature on mechanical properties
(a) tensile and yield strengths
(b) elongation at break and reduction in area
(c) prediction results of the C2P model
2.3.4 回火时间
控制淬火温度为950℃,淬火保温时间为30 min,回火温度为380℃,研究回火时间(30、60、90和120 min)对弹簧钢力学性能的影响,如图14所示。可见,随回火时间延长,材料的抗拉强度和屈服强度变化不大。当回火时间为90 min时,材料的塑性较好,因此选择90 min作为回火时间。另外,图14c给出了采用C2P模型预测的不同回火温度时的力学性能。可见,预测结果与实测结果的变化趋势基本一致,抗拉强度的预测误差绝对值在11.7~107.3 MPa之间,断后伸长率的预测误差绝对值在0~1.5%之间。
图14
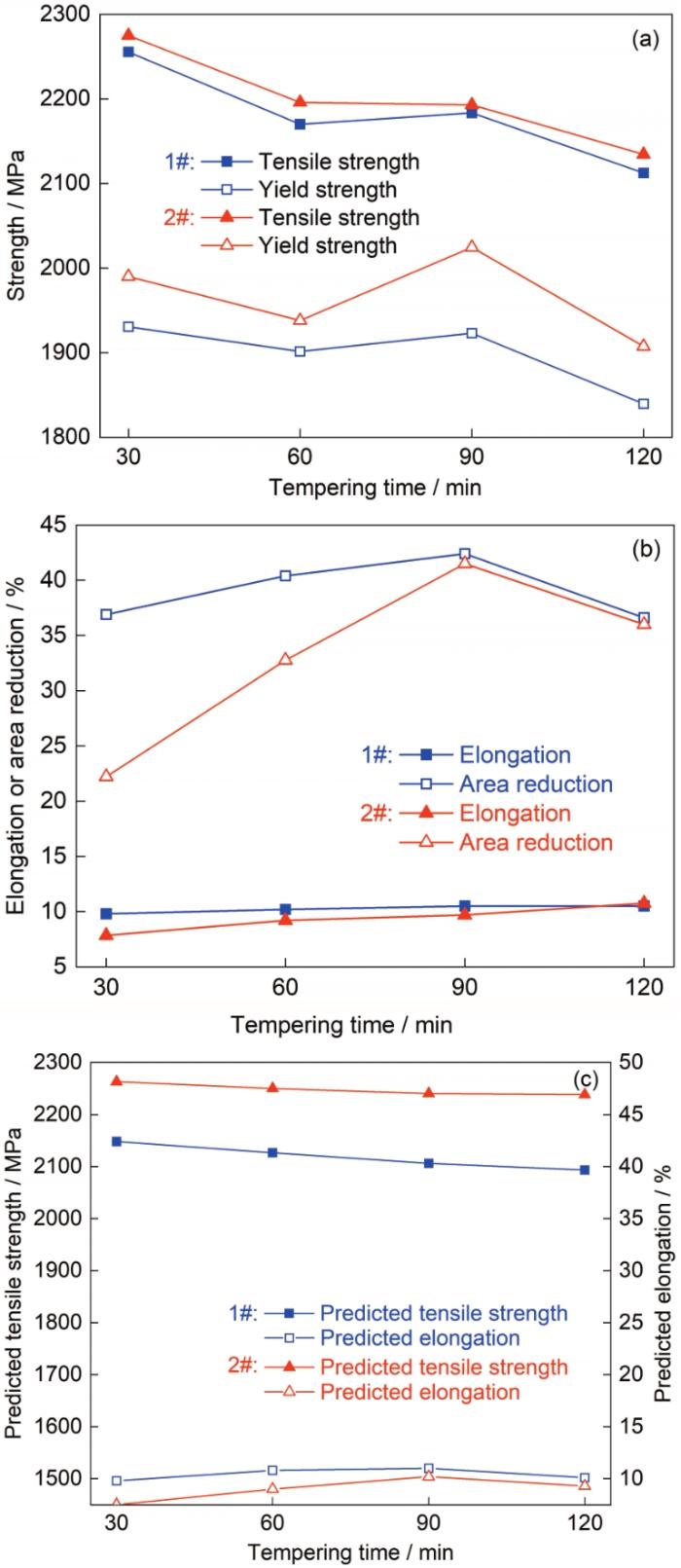
图14 回火时间对力学性能的影响
Fig.14 Effects of tempering time on mechanical properties
(a) tensile and yield strengths
(b) elongation after fracture and reduction in area
(c) prediction results of the C2P model
综上所述,优化后的热处理工艺为950℃保温30 min、油淬+ 380℃保温90 min、水冷,此时材料的强度和塑性均较好,1#钢的抗拉强度、屈服强度、断后伸长率和断面收缩率分别为2183.5 MPa、1923.0 MPa、10.5%和42.4%;2#钢的抗拉强度、屈服强度、断后伸长率和断面收缩率分别为2193.0 MPa、2024.5 MPa、9.7%和41.5%。2#钢的屈服强度高于1#钢,而塑性略低于1#钢。
3 分析与讨论
3.1 弹簧钢强化机理
弹簧钢的强化机理有多种,主要包括固溶强化、位错强化、晶界强化和析出强化。下面以950℃保温30 min、油淬+ 380℃回火90 min、水冷的试样为例,分析设计钢种的强化机理。
采用Fleischer公式估算固溶强化对屈服强度的贡献[20,21]:
式中,σss为固溶强化值;βi 为合金元素i的强化常数,其与该合金元素与Fe的晶格和模量错配相关,采用文献[22]中提供的数据;xi 为合金元素i的原子分数。需要说明的是,该公式默认C原子被马氏体板条边界的高密度位错捕获,因此没有考虑间隙原子的固溶强化作用;另外,由于V和Nb元素含量较低且大都以析出相的形式存在,因此没有考虑这2种元素的固溶强化作用。
根据XRD峰的半高宽计算马氏体位错密度及其对屈服强度的贡献,计算过程如下式所示[23~25]:
式中,σds为位错强化值;M为Taylor取向因子,取3;α为强化因子,取0.25;G为剪切模量,取80650 MPa;b为Burgers矢量模,α-Fe取0.248;ρ为位错密度;e为晶格应变;d为平均微晶尺寸;δ2θ为测量的XRD峰的半高宽;θ0为XRD峰的峰值角度;λ为Cu靶射线的波长,取0.1542 nm。
采用Hall-Petch公式计算晶界强化对屈服强度的贡献[26]:
式中,σgs为晶界强化值;KH为Hall-Petch强化系数常数,537 MPa/μm2,取自文献[27];de为晶粒尺寸,来自EBSD识别的有效晶粒尺寸(以15°取向差),1#和2#钢分别为0.44和0.52 μm。1#钢和2#钢晶粒取向的EBSD像如图15所示,图中黑线代表以15°取向差识别的界面。
图15
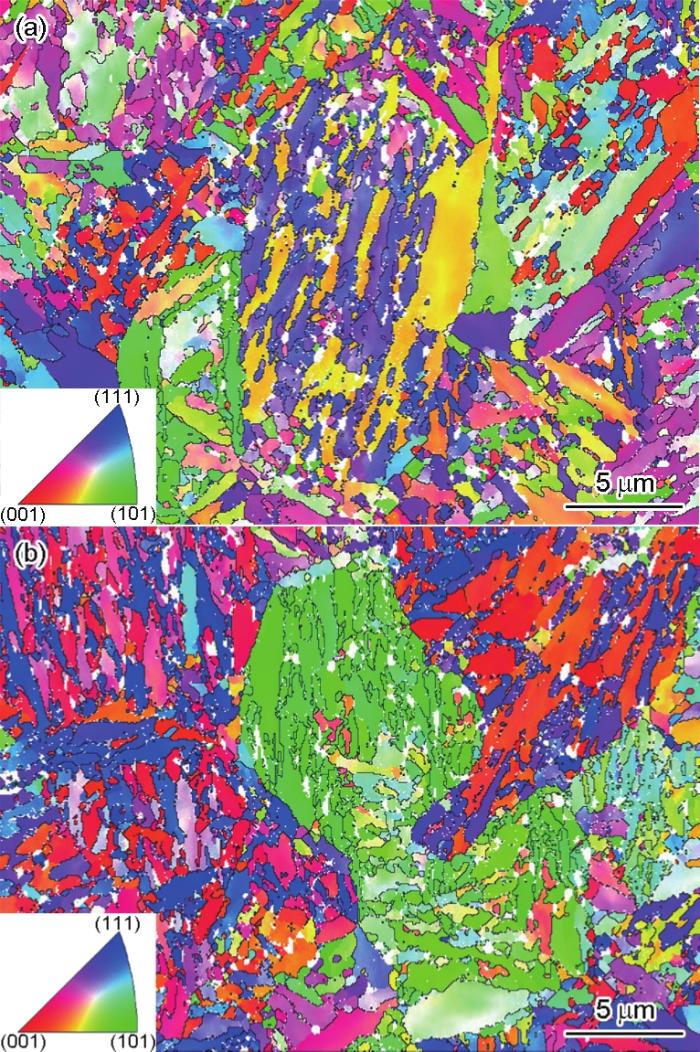
图15 1#钢和2#钢晶粒取向的EBSD像
Fig.15 EBSD grain orientation images
(a) 1# steel (b) 2# steel
采用Ashby-Orowan模型计算析出强化对屈服强度的贡献[28,29]:
式中,σps为析出强化值;rp为析出相的平均半径,fp为析出相的体积分数,均取自对碳膜复型试样中析出相的定量统计结果。1#钢和2#钢析出相形貌的TEM像和EDS分析结果如图16所示。1#钢中析出相主要为V的碳化物,同时含有少量的Nb、Cr、Mo和Mn;2#钢中析出相也主要为V的碳化物,同时含有少量的Cr、Mo和Mn。1#钢析出相的平均半径和体积分数分别为21 nm和0.19%,2#钢由于V含量较高,析出相的平均半径和体积分数有所增大,分别为27 nm和0.42%。
图16

图16 1#钢和2#钢碳膜萃取析出相的TEM像和EDS分析结果
Fig.16 TEM images (a, b) and EDS analysis results (c, d) of the precipitates extracted by carbon film for 1# steel (a, c) and 2# steel (b, d)
采用下式计算上述强化机理综合作用下的屈服强度[22]:
式中,σy为屈服强度;σ0为晶格摩擦应力,取50 MPa[30]。
各种强化机理的贡献及屈服强度的计算结果如图17所示。可见,晶界强化和位错强化起到主要作用,并且2#钢的晶界强化和析出强化高于1#钢,这使得2#钢具有更高的屈服强度。然而,屈服强度的计算值低于实验实测值,这可能与以下因素有关:第一,计算固溶强化时,Fleischer公式默认C原子被马氏体板条边界的高密度位错捕获,因而没有考虑C原子的固溶强化作用,然而回火后C原子必然发生一定的扩散,这可能导致固溶强化计算值偏低;第二,通过TEM观察发现,如图18所示,材料中存在一定量的孪晶,可起到孪晶强化作用,这在计算过程中没有考虑;第三,采用萃取复型的方法无法萃取到所有的碳化物,可能导致析出强化的计算值偏低。
图17
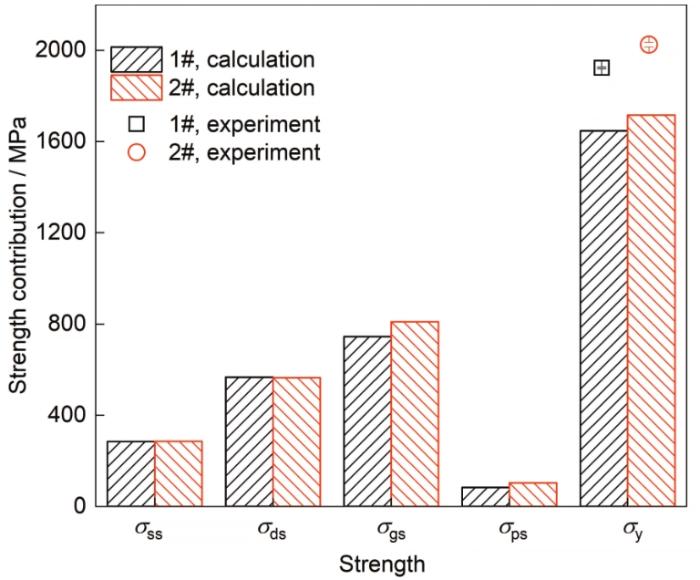
图17 各种强化机理对屈服强度的贡献
Fig.17 Contributions of various strengthening mechanisms to yield strength (σss—solid solution strength, σds—dislocation strength, σgs—grain boundary strength, σps—precipitation strength, σy—yield strength)
图18

图18 孪晶的TEM明场像和选区电子衍射花样
Fig.18 TEM bright field image and selected area electron diffraction pattern (inset) of the twin
3.2 弹簧钢塑性保持机理
弹簧钢在超高强度下仍可保持10%以上的断后伸长率和40%以上的断面收缩率,塑性良好。更有趣的是,随着回火温度的降低,强度逐渐升高,但塑性没有发生明显的下降,图19为1#钢和2#钢在不同温度回火后的拉伸曲线。一方面,该弹簧钢的晶粒较细,晶界强化在强化机制中贡献较大,较细的晶粒有利于协调变形,起到维持塑性的作用。另一方面,淬火后,钢中存在一定量的残余奥氏体和逆变奥氏体,380℃回火后的奥氏体TEM像和选区电子衍射花样如图20所示。一般认为,在钢中获得适宜含量的弥散奥氏体可抑制裂纹的扩展,有利于改善材料的塑韧性,另外还存在相变诱发塑性(TRIP)[31]和孪生诱发塑性(TWIP)[32] 2种增塑机制。另外值得注意的是,逆变奥氏体在合金元素含量较高的钢中比较常见,并形成于特定元素富集的区域,如马氏体时效钢中富Ni的区域[33]和中锰钢中富Mn的区域[34]。然而,本工作所开发钢种的合金元素含量较低,其在回火时仍然产生了一定量的逆变奥氏体,这种现象尚无相关文献报道,逆变奥氏体的形核机理及其对所开发钢种性能的影响值得进一步深入研究。
图19

图19 1#钢和2#钢在不同温度回火后的拉伸曲线
Fig.19 Tensile curves of samples with different tempering temperatures
(a) 1# steel (b) 2# steel
图20
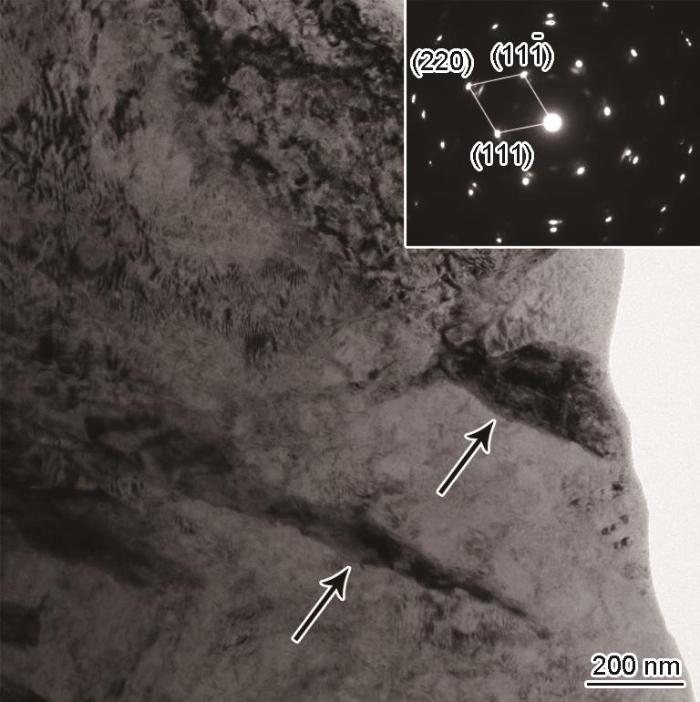
图20 奥氏体的TEM明场像和选区电子衍射花样
Fig.20 TEM bright field image and selected area electron diffraction pattern (inset) of austenite indicated by arrows
3.3 弹簧钢性能水平、经济性和工艺性分析
所开发钢种(热处理工艺:950℃保温30 min、油淬+ 380/400℃保温90 min、水冷)与文献[35,36]报道的60Si2CrVAT弹簧钢力学性能和合金元素含量对比如图21所示。新钢种的综合力学性能显著提升,且合金元素含量仅略有增大。在保持相同塑性水平(9%~12%)的前提下,抗拉强度由约1900 MPa提高至2100~2200 MPa,屈服强度由约1600 MPa提高至1850~2050 MPa。说明本工作开发的钢种具有显著的性能优势,有望作为下一代高速重载列车转向架弹簧以及大马力汽车减震器悬架弹簧的备选材料。
图21

图21 所开发钢种与文献[35,36]报道60Si2CrVAT的力学性能和合金元素含量对比
(c) alloying element content
Fig.21 Comparisons of mechanical properties and alloying element content between the developed steels and 60Si2CrVAT reported in Refs.[35,36]
(a) tensile strength and elongation after fracture
(b) yield strength and elongation after fracture
现有的2000 MPa级超高强度钢主要为马氏体时效钢[37~40],钢中一般含有质量分数为10%~20%的Ni和Co元素,而本工作开发的钢种的昂贵合金元素含量很低,总合金元素含量在5%以下,具有显著的成本优势。另外,本工作开发的钢种可采用钢铁企业线棒材的常规生产工艺生产,即常规冶炼-连铸-线棒材轧制,无需复杂的双真空(真空感应+真空自耗)冶炼工艺[39,41]。在热处理方面,本工作开发的钢种可通过简单的淬火+回火工艺实现,无需复杂热处理工艺,如淬火+碳配分+回火[42]、固溶+长时间时效[38,39]、多级时效[40]、铁素体/奥氏体循环相变[43]等,具有显著的工艺优势。
需要特别说明的是,特殊钢的性能要求复杂。对于弹簧钢来讲,表面脱碳敏感性、疲劳性能、耐蚀性能、抗氢致延迟断裂性能、抗弹性减退性能等都非常重要,一类新钢种的开发不能仅局限于强塑形指标的提高。本工作是新型超高强度弹簧钢开发的第一步,后续还将针对上述关键性能继续开展深入研究,以满足弹簧钢性能要求的复杂性和多样性。
4 结论
(1) 采用面向目标性能的机器学习设计系统(MLDS),结合实验优化,实现了超高强度弹簧钢化学成分和热处理工艺的快速研发。获得的2类钢种的抗拉强度分别为2183.5和2193.0 MPa、屈服强度分别为1923.0和2024.5 MPa、断后伸长率分别为10.5%和9.7%、断面收缩率分别为42.4%和41.5%。所开发钢种的合金元素质量分数低于5%,并可通过简单的淬火+回火工艺实现,具有显著的成本和工艺优势。
(2) 研究了淬火温度、淬火时间、回火温度、回火时间对所设计钢种显微组织和力学性能的影响。确定了较优的热处理工艺为950℃保温30 min、油淬+ 380℃回火90 min、水冷,可使材料获得较高的强度和良好的塑性。
(3) 所设计钢种的强化机理以细晶强化、位错强化为主,还存在一定程度的固溶强化、析出强化和孪晶强化。在380~420℃回火时,钢中产生了一定量的逆变奥氏体,可对材料的塑性起到有利作用。
来源--金属学报