分享:激光增材修复单晶高温合金的热裂纹形成机制
卢楠楠1, 郭以沫1,2, 杨树林3, 梁静静1, 周亦胄1, 孙晓峰1, 李金国,1
1
2
3
以第二代单晶高温合金DD432为研究对象开展激光增材修复实验,利用实验与理论计算相结合的手段,分析和研究了单晶高温合金在激光增材修复过程中的热裂纹形成机制。结果表明,单晶修复区内热裂纹在大角度晶界处形成,裂纹两侧呈现显著应力集中,裂纹源区域分布大量MC型碳化物。热裂纹的形成取决于液膜的稳定性、应力集中及碳化物析出相的共同作用。液膜稳定性取决于枝晶凝并过冷度,并与相邻晶粒间的晶界角度密切相关。基于Rappaz枝晶凝固过冷理论,计算获得DD432单晶合金形成稳定液膜的最小晶界角为2.9°,即该合金热裂纹形成的临界角;大角度晶界处的枝晶凝并过冷度为395 K,远高于晶粒内部枝晶间液膜的过冷度(29.58 K)以及小角度晶界(3.6°)处的枝晶凝并过冷度(56 K),大角度晶界为开裂提供了稳定液膜;沉积区内部的高水平应力集中驱动了热裂纹的萌生与扩展;MC型碳化物析出相通过“钉扎作用”抑制液相补缩及弱化与基体之间结合强度等作用进一步促进了热裂纹形成。
关键词:
随着世界航空工业的高速发展,用于制造航空发动机中热端部件的镍基高温合金得到了广泛应用,其中镍基单晶高温合金由于去除了横向及纵向晶界,获得了优异的高温抗蠕变、抗疲劳及抗腐蚀性能,已成为涡轮叶片的首选材料[1~3]。单晶合金涡轮叶片长期服役于高温、高压、高载荷等苛刻环境下,会发生磨损、开裂、掉块等形式的损伤,导致叶片失效报废[4,5]。由于单晶叶片的制造成本高昂、制造周期长,国际发动机OEM (原始设备制造商)厂商通常对受损叶片进行修复,以延长其使用寿命的同时大幅降低使用成本。因此,发展单晶涡轮叶片的修复技术具备重要的战略及经济意义。
激光增材制造技术凭借其“精准定位、可控增材”的特性及适宜单晶外延生长的超高温度梯度条件,成为最有前景且绿色高效的单晶涡轮叶片修复技术[6~9]。目前,单晶叶片激光增材修复技术仍面临两大瓶颈问题[10~14]:(1) 修复区极易形成杂晶,难以保证单晶完整性;(2) 修复区热裂纹缺陷频发。杂晶的存在会显著恶化单晶高温合金的高温力学性能,热裂纹缺陷则直接导致单晶修复失效,故需首要解决单晶增材修复过程中的热裂纹问题。研究[15~17]表明,合金中Al和Ti 2种元素的含量总和可以用于衡量该合金的可焊性(热裂敏感性),其中Al + Ti含量≥ 4.5% (质量分数,下文除特别注明,均指质量分数)的合金具备很高的热裂敏感性,通常被看作不可焊的合金。为确保具备足够的高温性能,高温合金中的γ'-Ni3(Al, Ti)强化相含量需要维持在50%~80% (体积分数)[18],造成合金设计时Al、Ti 2种元素的添加总量高于4.5%,最终导致这类高性能高温合金具有极高的热裂倾向。近期,已有多项工作聚焦于IN738[19]、CM247LC[20]、Rene 104[21]等牌号合金的热裂纹研究,这几种典型的高性能高温合金中Al、Ti含量的总和均超过4.5%,以致在焊接过程中均具备极高的热裂倾向。上述研究表明,热裂纹通常发生于凝固末期残留液相薄膜的区域,液相薄膜两侧存在拉应力时导致液膜处发生撕裂并形成裂纹[22]。然而,以上合金均为多晶材料,其显微组织结构和单晶合金存在较大区别。目前针对高Al、Ti含量单晶高温合金的热裂纹研究较少,Wang等[14]和Rong等[23]发现激光重熔DD6和MC2单晶合金中超过16°的晶界处才会形成热裂纹;Zhou等[7]则对增材制造单晶合金CSU-B1块体试样的开裂行为进行研究,发现大角度晶界处的裂纹敏感性更高,还会与析出相有一定关联。然而,上述单晶裂纹的研究主要围绕激光表面重熔或者增材制造块体试样,缺乏对晶界、应力及析出相等多因素的影响研究。此外,类似于空心叶片的薄壁结构试样,其与块体试样的组织尤其是应力分布特征有显著差异,这类薄壁结构试样热裂机制亦有待揭示。因此,有必要对单晶高温合金薄壁结构在增材修复过程中的开裂行为及裂纹萌生扩展机制进行深入研究。
本工作针对第二代单晶高温合金DD432开展激光增材修复研究,分析了单晶高温合金激光增材修复区热裂纹及相邻区域的组织形貌特征,重点探究激光熔池在凝固末期的液膜稳定性、残余应力分布及元素偏析等因素对热裂纹的影响规律,进一步揭示热裂纹形成机制。
1 实验方法
本实验选用镍基单晶高温合金DD432材料制备的基材和填充粉末,该合金的主要化学成分(%)为:C 0.12~0.18,Cr 4.3~5.6,Co 8~10,W 7.7~9.5,Mo 0.8~1.4,Al 5.6~6.3,Nb 1.4~1.8,Ta 3.5~4.5,Re 3.5~4.5,Ni余量。基材采用高速凝固法(HRS)定向凝固技术制备尺寸为10 mm × 70 mm × 200 mm的单晶试板,为了缓解枝晶间的元素偏析问题,对DD432单晶试板进行了固溶热处理,热处理工艺为:1280℃、4 h、空冷(AC) + 1290℃、4 h、AC。随后,利用线切割将单晶试板切成3 mm × 5 mm × 40 mm单晶基材试样,利用600号金相砂纸对待修复表面进行打磨并置于丙酮中进行超声清洗。粉末由Ar气雾化法制备,粉末粒径为45~120 μm。在进行单晶合金激光增材修复实验前,先将粉末放入真空烘干箱完成烘干,温度80℃、烘干时长24 h。
激光增材修复实验由中国科学院金属研究所自主研发的激光定向能量沉积设备完成,设备由CP4000横轴流CO2激光器、Siemens数控机床、SL400水冷机、送粉器及同轴环形送粉喷嘴构成,实验全程在Ar气环境下完成。激光功率设定1200 W,扫描速率0.015 m/s,送粉速率4.5 g/min,激光在基材(001)表面沿[100]方向进行扫描,采用层间往复连续沉积策略。
金相试样首先利用600~3000号砂纸依次进行打磨,随后分别利用2.5和1 μm的金刚石抛光液进行抛光,最后应用0.04 μm的硅溶胶悬浮液完成最终抛光。对金相试样进行腐蚀以分析组织形貌,腐蚀液成分为100 mL H2O + 100 mL HCl + 20 g CuSO4,腐蚀时间10 s。用于取向分析的试样需要进行电解抛光,抛光液为90 mL C2H6O + 10 mL HClO4,电解抛光温度-25℃,电流10 mA,电解抛光持续时间30 s。采用DM4M金相显微镜(OM)观察试样显微组织,采用配备Oxford能谱仪(EDS)的Apreo2C场发射扫描电镜(SEM)观察试样显微组织并进行成分分析,其中二次电子(SE)及背散射电子(BSE)像用于表征裂纹及周边组织形貌。晶体取向信息则通过SEM配备的AZtec EBSD (电子背散射衍射)系统完成获取,工作电压20 kV,工作距离15 mm,取向数据检测的步长设置为1~3 μm,所获取向数据利用Channel 5软件进行处理。
2 实验结果
2.1 沉积区裂纹特征
图1展示了DD432单晶高温合金激光增材修复试样中沉积区的裂纹宏观形貌,可见近似平行建造方向的3条纵向裂纹。裂纹1最为严重,长度达40 mm,并与裂纹2联合贯穿整个沉积区;裂纹3则位于沉积区的中上区域,裂纹长度接近30 mm。图2为沉积区内部的裂纹形貌,可以观察到修复区内部的组织为列状生长的柱状树枝晶组织,局部区域形成了杂晶晶粒。裂纹分布于杂晶的晶界处,呈现出沿晶开裂的特征,同时未发现穿晶断裂特征。此外,图2显示出裂纹源处于相邻沉积道次之间的界面处,由于相邻的道次界面区域通常受到后续沉积过程的热作用,导致该区域的温度接近甚至超过合金的熔点,引发局部区域发生重熔并促进裂纹的形成。基于以上裂纹形态及分布特征初步判断沉积区内部的纵向裂纹为热裂纹。为确定裂纹的类型,需对裂纹的断口形貌进一步表征。图3a为纵向裂纹的断口形貌,可见断口呈现出近似“糖葫芦”状的特征,表明该断口是由具有发达二次枝晶臂的树枝晶在枝晶间区域开裂形成的;图3b进一步展示出裂纹两侧分布着液相薄膜,因此可以证明本实验中的裂纹类型为热裂纹。
图1

图1 DD432单晶高温合金激光增材薄壁试样的宏观裂纹形貌
Fig.1 Macro-morphology of cracks in the additive manufactured DD432 single crystal (SX) superalloy thinwall specimen
图2
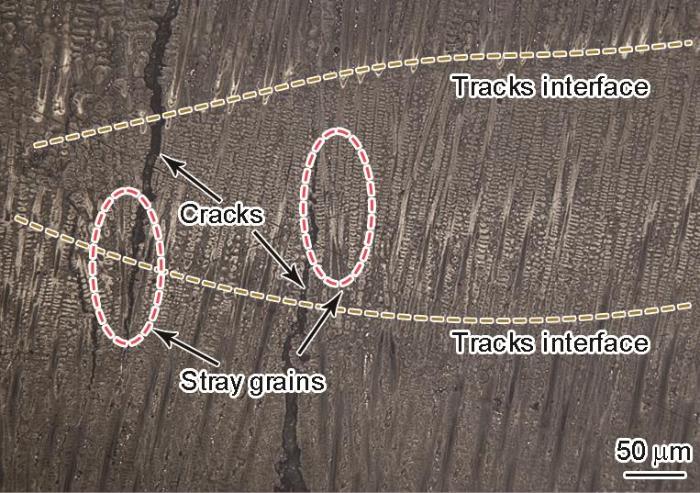
图2 沉积区纵截面裂纹微观形貌的OM像
Fig.2 OM image of micromorphology for longitudinal section cracks in the deposition
图3

图3 纵向裂纹断口形貌及裂纹尖端液膜分布的SEM像
Fig.3 SEM images of longitudinal crack fracture morphology (a) and liquid film distribution at the crack tip (b)
2.2 裂纹源特征分析
图4为纵向裂纹源尖端区域的组织形貌及取向特征。可以看出,裂纹源周边区域存在数个细小光滑的圆形孔洞,孔洞尺寸为20~30 μm,如图4a中箭头所示,根据上述特征可判断此类孔洞为气孔。裂纹源尖端并未发现气孔或其他缺陷存在,纵向裂纹萌生于呈发散角的2组柱状晶之间,并沿该发散晶界扩展开裂。图4b~d分别为沿X、Y、Z 3个方向上的取向分布图。可见,沿Y方向枝晶取向近乎平行[001]晶向(图4c),但沿X方向及Z方向则呈现出明显的颜色差异,即X与Z方向的晶体取向具有明显的取向差。以沿Z方向为枝晶的主轴方向,从图4d中可以发现裂纹左右两侧的柱状晶呈发散生长特征。分别对不同柱状晶晶界处的取向差进行检测(具体选取位置及晶界见图4d),可以看出,裂纹源处的晶界角度在21.3°~30°之间,属于发散型大角度晶界。分别在左右两侧额外选取了更大角度的大角度晶界(39.4°、39.7°),均未发现显微裂纹萌生。此外,右侧柱状晶区域选取的3.6°及4.2°小角度晶界处亦未发现显微裂纹的存在;左侧柱状晶区选取的16.8°大角度晶界也未发现显微裂纹。综上分析,可以得出在凝固末期热裂纹在大角度晶界处更容易萌生扩展,而在小角度晶界处或40°以上的大角度晶界处则较难形成。
图4
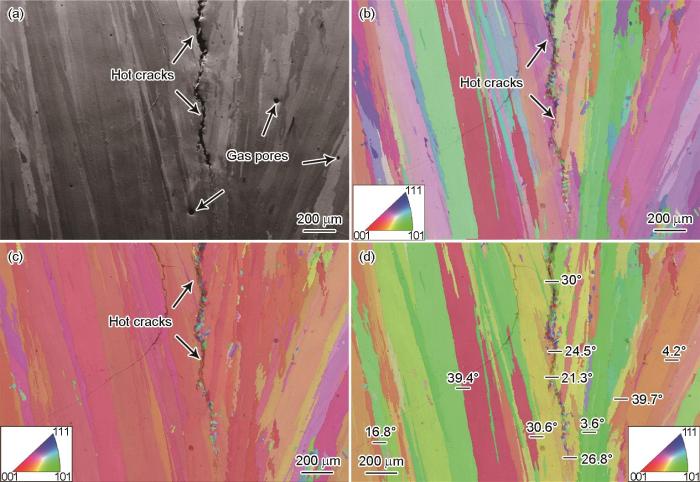
图4 裂纹源区域组织形貌及取向特征
Fig.4 Morphology and orientation characteristics of the crack initiation region
(a) back scattered electron (BSE) image of the crack initiation region
(b-d) inverse pole figures (IPFs) along the X (b), Y (c), and Z (d) directions, respectively
为进一步明晰热裂纹萌生扩展规律,除了分析晶界角外还需探究残余应力的影响。图5为应用EBSD获得的裂纹源区域局部取向差(KAM)分布图。基于晶体的晶格畸变检测,KAM图可以直观展示待测区域的应变信息云图,判断应力分布规律。从图5可见,裂纹源处的发散大角度晶界存在显著的应力集中,这里将该区域定义为高应变区,如图中白色虚线框所示。将图4d中选取的晶界角位置及角度绘制到图5中,如橙色标记所示。可以看出,两侧柱状晶区内的3.6°及4.2°小角度晶界处均存在应力集中,39.4°和39.7° 2组大角度晶界处则未形成应力集中,其中20°~30°发散晶界处应力集中最为严重。尽管小角度晶界处存在应力集中,但是小角度晶界却无法形成裂纹;40°及以上的大角度晶界虽然热裂倾向大,但是晶界处无应力集中亦无法形成热裂纹。
图5
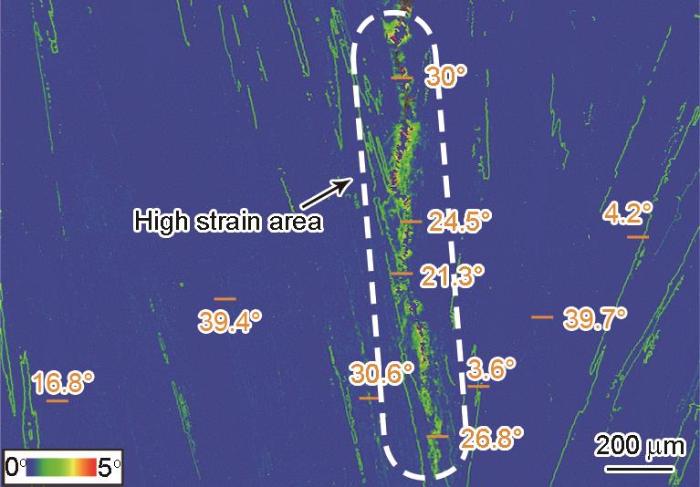
图5 裂纹源区域局部取向差(KAM)分布图
Fig.5 Kernel Average misorientation (KAM) map of the crack initiation region
为了确定热裂纹的形成是否存在其他影响因素,进一步对裂纹源尖端区域进行分析,如图6所示。针对图6a中裂纹源的尖端选取区域进行高倍表征,选取位置如图6a中虚线框。图6b为该放大区域的BSE像,利用Channel 5后处理软件绘制晶界分布图(如图6b),图中蓝色实线代表5°~15°的小角度晶界,红色实线代表15°以上的大角度晶界。可以看出裂纹萌生于大角度晶界处,小角度晶界处无裂纹形成。图6c~e分别展示了沿X、Y、Z 3个方向上的晶体取向分布特征,可见图像中央的完整晶粒与相邻晶粒间出现了局部开裂的现象,即热裂纹萌生于该晶界处。对2个晶粒间的取向差进行分析表征,选取位置及晶界角度见图6e中标注。从图中可见,2个晶粒间的晶界角度范围在20°~26°之间,与上述低倍下观测到的裂纹所处晶界角范围一致。该区域对应的KAM分布图显示出局部裂纹萌生处具有显著的应力集中,左侧区域也存在较为明显的应力集中。由图6e和f可见,左侧应力集中区域对应3.1°小角度晶界。结合裂纹源区域低倍和高倍的组织取向特征可知,热裂纹受到晶界角和应力集中的共同作用。当凝固末期形成的大角度晶界处具备高水平的应力集中才会导致热裂纹的萌生,而有应力集中的小角度晶界处或者无显著的应力集中的大角度晶界处则不会形成热裂纹。
图6
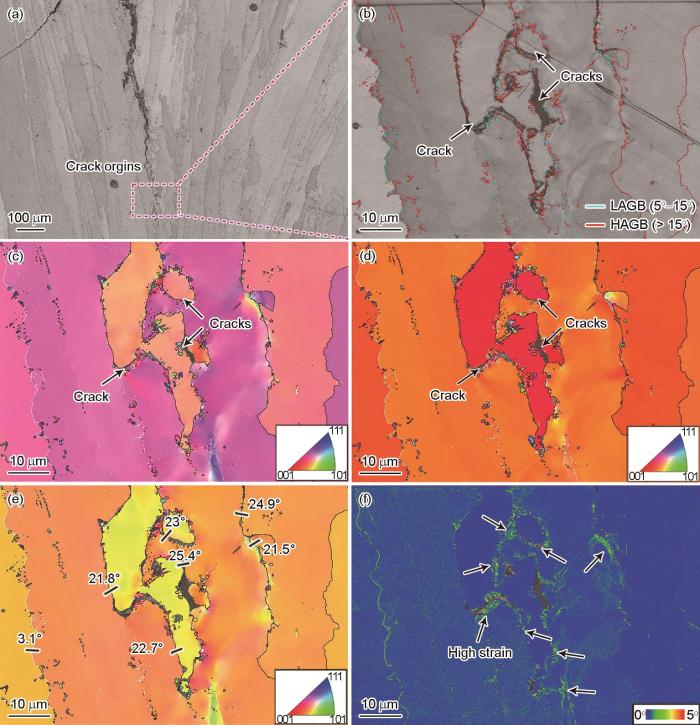
图6 裂纹源区域局部放大组织及取向特征
Fig.6 Localized amplified microstructure and orientation characteristics in the crack source region (HAGB—high-angle grain boundary, LAGB—low-angle grain boundary)
(a) BSE image of the crack initiation region
(b) enlargement of the selected area in Fig.6a
(c-e) IPFs along the X (c), Y (d), and Z (e) directions, respectively
(f) KAM map of the selected area in Fig.6a
针对裂纹源局部区域进行观察,发现裂纹萌生区域存在显著的元素偏析现象。图7为裂纹源区域(图6b)的合金元素面分布图,可以看到Mo、Ta、Nb、Al、C、W等元素在裂纹萌生位置出现显著的偏聚,而对应位置的Re元素则出现明显贫化。图7中元素的偏析呈现出小块状或类字母型的特征,表明在裂纹萌生的位置存在富含上述几种元素的析出相,初步分析可能为碳化物析出相。为证实上述碳化物析出相的假设,对试样多条裂纹的萌生区域进行EDS检测,发现均具有相似的析出相特征。图8为裂纹萌生处的BSE像及EDS分析。可见,裂纹萌生处分布白色析出相,形状为块状及近似字母的长条状,EDS结果(图8b)表明,白色析出相富集Nb、Ta及C 3种元素,结合其形貌可知白色析出相为MC型碳化物。其他单晶高温合金的增材制造相关研究工作[24]也证实了MC型碳化物的存在。上述碳化物分布规律表明,碳化物对热裂纹的形成有一定影响。综上分析可以得出,单晶高温合金激光增材修复过程中热裂纹形成的影响因素主要有晶界角、应力集中及碳化物的分布。
图7

图7 裂纹源局部区域元素面分布
Fig.7 Elemental distribution in the crack source region
图8

图8 裂纹萌生处的组织形貌的BSE像及EDS分析
Fig.8 BSE image of microstructure (a) and EDS analysis of point 1 (b) near crack initiation
3 分析讨论
热裂纹的萌生及扩展实际上是由应力集中和液相薄膜共同作用的结果[22],其中液相薄膜的稳定性决定了其在凝固末期的维持时间,液膜稳定性越高则热裂倾向也相对更高;应力集中则为裂纹萌生和后续扩展提供了驱动力,仅当液膜两侧具备拉应力条件裂纹才可形成;析出相则影响界面结合强度或促进稳定液膜的形成[25]。因此,本节分别从液膜稳定性、应力集中及碳化物析出相3个方向来分析热裂纹的形成机制。
3.1 液膜稳定性
由于稳定的液膜是热裂纹形成的必要条件,因此首先探讨液膜的稳定性及其影响因素。由于单晶合金在凝固过程中以树枝晶形态生长,在凝固末期根据固相分数的不同,液相具有3种存在形式[14]:(1) 当固相的体积分数(fs)低于90%时,液相以通道形式存在;(2) 当fs处于90%~94%范围内,液相以薄膜形式存在;(3) 当fs高于94%直到完全形成固相时,液相以微小液滴形式存在。上述3种形式的液相中,液相以液相通道形式存在时,一旦发生开裂,远端的液相将对裂纹实现填充完成自愈合;当液相以小液滴形式存在时,固相骨架已完全联通,残余应力将通过固相骨架传递释放,同时固相骨架的强度基本与完全固相相似,因此也难以形成热裂纹;最终只有形成液相薄膜并且液膜两端存在高水平拉应力才可导致热裂纹的形成,其对应的固相分数范围90% ≤ fs ≤94%也被称为热裂敏感区间。
前期已有研究[26]发现液膜的稳定性实际上与晶界角度有关,提出了著名的枝晶凝并理论:晶界可分为“排斥”晶界与“吸引”晶界两大类,当相邻晶粒间形成“吸引”晶界时,枝晶发生凝并促进液膜转化为孤立小液滴,因此无法形成裂纹;当相邻晶粒形成“排斥”晶界时,连续液膜会一直维持到较低的温度,直到最后全部形成固相为止,这类“排斥”晶界有可能引发热裂纹的形成。为此,Rappaz等[27]提出了枝晶凝并过冷度ΔTb以衡量液膜的稳定性:
式中,γgb为晶界能;γsl为固/液两相之间的界面能;ΔSf为材料的熔化熵;δ为溶质扩散层的厚度(取1 nm)。令
由
式中,G为剪切模量;b为Burgers矢量模;
表1 计算枝晶凝并过冷及晶界能所需的热物理参数[29~31]
Table 1
Physical parameter | Value | Unit | Ref. |
---|---|---|---|
Shear modulus G | 86.3 | GPa | [29] |
Burgers vector b | 3.578 × 10-10 | m | [30] |
Solid/liquid interfacial energy γsl | 310 | mJ·m-2 | [31] |
Poisson ratio ν | 0.467 | - | [29] |
为了衡量不同晶界角度对应的液膜稳定性,需要计算液膜可维持的最低温度,这里可利用下述公式计算获取“吸引”晶界及“排斥”晶界与凝并过冷度之间的关系[25,27]:
式中,
式中,Tm为合金熔点,Tl为合金的液相线温度,k为溶质平衡分配系数。DD432合金相应的参数取值如下[29]:Tm = 1726 K,Tl = 1670.15 K,Ts = 1635.15 K,k = 0.61。联立式(
图9
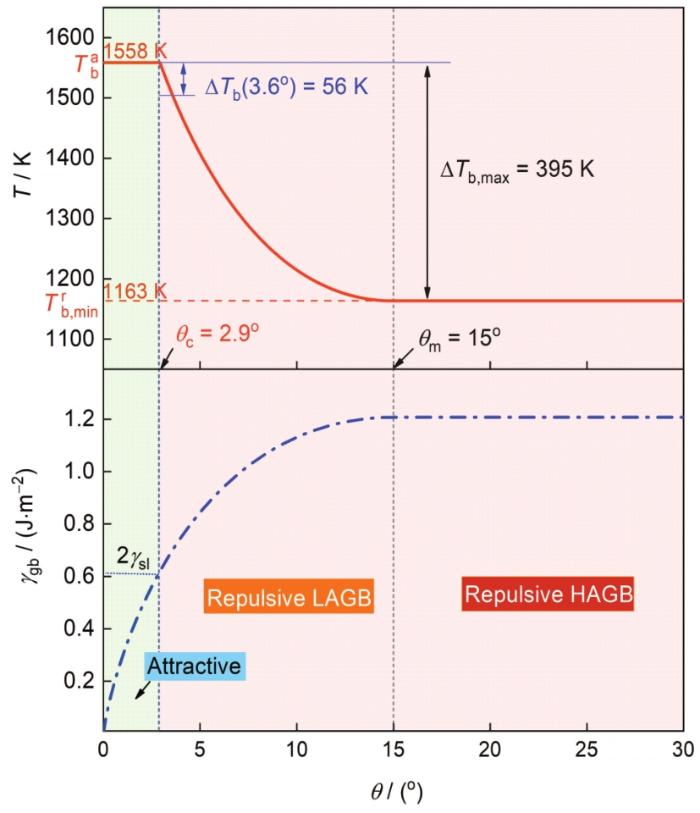
图9 晶界角与枝晶凝并温度及晶界能之间的关系
Fig.9 Relationships between GB angle (θ) and the dendrite coalescence temperature and GB energy (γgb) (T—temperature, θc—critical transition angle, θm—the angle corresponding to the maximum GB energy,
液膜除了存在于晶界区域,晶粒内部的枝晶间区域也会存在液膜。为此还需分析枝晶间区域液膜的过冷度。由于液膜仅在固相分数为90%~94%区间内,应用
图10

图10 DD432单晶高温合金凝并温度与固相分数之间的关系
Fig.10 Relationships between the solidification temperature and the solid fraction (fs) for DD432 SX superalloys (ΔTDD432—interdendritic liquid film undercooling in DD432 alloy)
3.2 热裂纹驱动力
类似焊接过程,增材制造过程中沉积区会在热收缩及凝固收缩作用下形成残余应力[33]。由于增材制造为多层沉积累加的过程,基材或者已凝固的沉积层会在当前沉积层冷却过程中受到压缩作用,而在内部形成压应力,反之当前凝固的沉积层中将形成拉伸应力。Frenk等[34]证实了增材制造过程中沉积区内部分布有残余拉伸应力,并指出随着沉积层数的增加这种拉应力会逐渐增大,直到一定层数后维持稳定。Mukherjee等[35]采用模拟方法计算出增材区内部的应力分布,提出残余的拉应力主要分布于增材区内部,尽管局部层间会形成压应力,但整体仍呈现拉应力特征。在此基础上,一旦增材区的拉应力超过凝固末期的固相与液膜间的强度,热裂纹便会形成。增材区内部的拉应力驱动热裂纹的萌生和扩展。对于单道多层沉积的薄壁结构,在平行于激光扫描方向及建造方向的纵截面上的拉应力最为显著,这也是纵向界面出现严重纵向裂纹的原因。
图5的分析结果表明,应力并不是均匀分布于沉积区内部,而是呈现应力集中现象,即增材修复区内部的拉应力集中才是驱动热裂纹萌生扩展的本质原因。在凝固过程中,应力会通过固相骨架实现传递,一旦遇到液膜便会在该区域形成应力集中,当应力集中超过液膜强度后便会发生撕裂形成热裂纹[36]。为了快速判断液膜处的应力集中大小,可通过单个枝晶间液膜的局部应变因子(fstrain)定性分析,具体关系式如下[14]:
式中,λ为树枝晶的一次枝晶间距(本实验中λ = 15 μm),δ取1 nm。应用
3.3 碳化物析出相的影响
由于DD432单晶高温合金中含有0.12%~0.18%的C元素,定向凝固及增材制造制备的合金内部均会形成较多MC型碳化物,其形态多呈现鱼骨状或字母状。依据DD432单晶合金的成分组成,常见的MC型碳化物包括NbC、TaC、MoC、WC等[37]。这与本实验测得的Nb、Ta、Mo、W、C等元素在晶界处偏析现象一致,进一步证实了本实验中MC型碳化物分布于裂纹源区域。MC碳化物对热裂纹的影响主要分为2方面:(1) MC碳化物促进液膜的形成;(2) MC碳化物降低了凝固末期材料的结合强度。
在单晶合金的凝固末期,通常情况下只有固相分数在90%~94%区间内才可形成连续液膜,当固相分数低于90%时,由于晶界处液相通道的存在,远端液相可以实时填充被拉开的晶界,无法形成液相薄膜。当晶界两侧分布大量MC碳化物时,由于碳化物较高的熔点无法被晶界处液相重熔而完整保留,相反这些碳化物又会阻碍远端液相的流动,类似“钉扎作用”抑制远端液相的补缩,最终导致固相分数低于90%条件下也可能形成液膜,提高了热裂纹形成倾向。
另一方面,碳化物属于硬脆相,其与基体γ相之间的热膨胀系数存在显著差异。因此,在凝固末期的高温条件下碳化物与基体γ相的界面强度相比γ相之间的界面强度存在一定程度的降低。当该区域有应力集中时,碳化物与基体γ相界面处会优先发生开裂,促进了热裂纹的形成。
4 结论
(1) 激光增材修复DD432单晶高温合金表现出很强的裂纹敏感性,沉积区内部形成纵向裂纹,裂纹断裂面呈现发达枝晶形貌,属于热裂纹。沉积区热裂纹萌生于大角晶界处,裂纹周边存在显著的应力集中,同时裂纹源处分布MC型碳化物析出相。热裂形成由液膜稳定性、应力集中、碳化物析出相3个因素决定。
(2) 液膜稳定性取决于枝晶凝并过冷度,并与相邻晶粒间的晶界角度密切相关。基于Rappaz枝晶凝并理论计算获得连续液膜形成的最小临界晶界角θc为2.9°。大角度晶界处的液膜过冷度(395 K)显著高于小角度晶界(3.6°)液膜过冷度(56 K)及晶粒内部枝晶间区域的液膜过冷度(29.58 K),沉积区内部的大角度晶界处液膜稳定性最高,最易形成热裂纹。
(3) 激光增材修复的多层沉积过程导致修复区内部形成残余拉应力,晶界液膜处呈现显著应力集中特征。晶界处液膜在两侧拉应力作用下发生撕裂导致热裂纹萌生,该应力又为后续裂纹沿晶界扩展提供驱动力。
(4) DD432单晶高温合金快速凝固过程中Nb、Ta、Mo、W、C等元素在晶界处发生偏析,在晶界两侧形成细小鱼骨状MC型碳化物析出相,该析出相对远端液相形成“钉扎作用”抑制了液体的补缩,提高了晶界处液膜稳定性;此外,晶间碳化物的形成亦会弱化高温下晶界强度,最终促进热裂纹的形成。
来源--金属学报