分享:铝合金搅拌摩擦焊接头微观组织及缺陷的金相表征
摘 要:从接头低倍形貌、各区域微观组织特征以及缺陷特征3个方面对铝合金搅拌摩擦焊接头的金相表征进行了介绍和总结.结果表明:接头低倍形貌有河床型、鼓型以及壶嘴型等3种;接头各区域微观特征可从再结晶和第二相分布两个方面进行分析;洋葱环缺陷实质是大小不等的再结晶晶粒或数量不同的弥散析出相质点交替分布而形成的;Z型线缺陷是原始界面上氧化膜弥散分布而形成的;吻接缺陷和钩状缺陷是一种假性连接缺陷;孔洞和隧道型缺陷主要是由焊接过程中热输入量不够而导致的.
关键词:搅拌摩擦焊;铝合金;金相表征;低倍形貌;微观组织;缺陷
中图分类号:TG44 文献标志码:A 文章编号:1001G4012(2018)06G0431G07
搅拌摩擦焊是英国焊接研究所于1991年发明的一种新型固相连接技术,焊接最高温度不超过材料熔点,材料只达到塑性化状态,可避免传统熔化焊容易出现的气孔和热裂纹等缺陷,非常适用于低熔点有色金属如铝合金、镁合金等的焊接.材料宏观上的力学性能是由材料的微观组织结构决定的,因此透彻地分析和研究搅拌摩擦焊接头的微观组织及缺陷的情况,可以有针对性地改善工艺,有效地提高搅拌摩擦焊接头的宏观性能.
笔者主要从接头低倍形貌、各区域微观组织特征以及缺陷特征3个方面对铝合金搅拌摩擦焊接头的金相表征方法进行了介绍,以供相关人员参考.
1 焊接接头低倍形貌的金相表征
搅拌摩擦焊的焊接工艺参数主要包括搅拌头外形轮廓、焊接压力、焊接速度、焊接转速等.焊接工艺参数的不同会形成不同的焊接接头低倍形貌.焊接接头低倍形貌主要有上宽下窄的河床型、上下宽度相近的鼓型以及上尖下圆的壶嘴型3种,见图1.
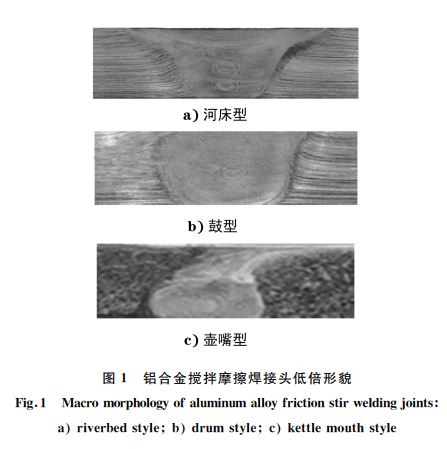
一般来讲,焊接速度一定,焊接转速低,形成河床型;转速增加,形成鼓型.这是因为焊接转速低,焊接热输入量低,焊接接头上部受轴肩影响面积较大,焊接接头下部受搅拌针影响面积较小,从而形成上宽下窄的河床型;转速增加,焊接热输入量也增加,受搅拌针影响的面积增大,因此形成上下宽度相近的鼓型[1].MA 等[2]的研究表明了同样的规律:在低焊接转速下,焊核区为盆状(即河床型),随着焊接转速的提高,焊核区变成椭圆形(即鼓型).壶嘴型低倍形貌的形成,是各种参数综合作用的结果,它是轴肩搅拌区和搅拌针搅拌区这两个区域差别比较明显时形成的一种低倍形貌.2 焊接接头各区域微观组织的金相表征铝合金搅拌摩擦焊接头可以划分为不同的区域,各区域微观组织具有不同的特征,具体表现为再结晶情况的不同以及第二相分布情况的不同.
2.1 搅拌摩擦焊接头区域划分
搅拌摩擦焊接头主要分为:焊核区(NZ)、热机影响区(TMAZ)、热影响(HAZ)和母材(BM)共4大区域[3].焊核区被充分搅拌并塑性化,受到强烈的力和热的作用,热机影响区受到的力和热的作用次于焊核区,热影响区仅受到热的作用,母材则不受任何热和力的作用.焊核区又可细分为:上部轴肩搅拌区,主要受到轴肩的锻压作用;下部搅拌针搅拌区,主要受到搅拌针的搅拌作用.
热机影响区从图2的左右方向上可分为:前进侧热机 影 响 区 (TMAZGAS)和 后 退 侧 热 机 影 响 区(TMAZGRS).所谓前进侧是指搅拌工具旋转切线方向与焊接速度方向一致,而后退侧则相反.
热机影响区从图2的上下方向上又分为:焊核轴肩搅拌区的热机影响区和焊核搅拌针搅拌区的热机影响区.轴肩搅拌区的热机影响区受到的热和力的作用较大,与焊核界限不明显;搅拌针搅拌区的热机影响区受到的热和力的作用较小,与焊核界限较明显.低倍下各区域的部位标识见图2.
2.2 各区域微观组织再结晶情况的表征分析
7020GT6铝合 金 母 材 晶 粒 呈 轧 制 的 拉 长 粗 晶粒,见图3a).
焊核区在热和力的作用下,原始粗晶粒被破碎成多边形小晶粒,在热的作用下,获得足够能量的破碎小晶粒将发生再结晶,形成光滑边界的再结晶晶粒.整个焊核各处的温度是不均匀的,温度较高及持续时间较长区域的再结晶晶粒会发生长大;而温度相对较低,能量不够发生再结晶的区域,会残留少量破碎后的多边形小晶粒.因此,焊核区主要是细小再结晶晶粒,再结晶晶粒有些会发生长大,也会存在少量破碎的未发生再结晶的小晶粒.7020GT6铝合金焊核区典型微观组织形貌见图3b),主要为细小等轴再结晶晶粒.热机影响区的表征,首先要区分前进侧和后退侧:前进侧搅拌针搅拌区的热机影响区与焊核区的分界线非常明显;后退侧两者的分界线则相对模糊一些,存在较窄的过渡区.这是因为在搅拌头的旋转摩擦作用下,前进侧热塑性金属几乎即刻便被搅拌头挤压出去,该部分温度冷却快,因此焊核和热机影响区的分界线明显.后退侧热塑性金属有一个流动过程,焊核和热机影响区之间存在温度过渡,因此分界线相对前进侧的不太明显.前进侧轴肩搅拌区的热机影响区由于受到轴肩、影响,能量较高,热机影响区较宽,与焊核间呈过渡特征,界限不明显,一般不作特征性的分析.重点分析前进侧搅拌针搅拌区的热机影响区的再结晶情况,该区域原始粗晶粒在力的作用下明显弯曲,部分长晶粒断裂成几段,在能量较高的部分晶界处发生了再结晶,形成了细小的再结晶晶粒.部分晶粒内部发生了回复,在大晶粒内部形成了网络状的细小亚晶粒.7020GT6铝合金搅拌摩擦焊接头前进侧热机影响区的典型形貌见图3c),可见原始粗晶粒弯曲变形,部分晶界上可观察到细小的再结晶晶粒,部分大晶粒内部可观察到亚晶.后退侧的轴肩搅拌区热机影响区与前进侧的一样,也相对较宽,界限不明显,一般不作特征性的分析.后退侧搅拌针搅拌区热机影响区与焊核界限相比前进侧的不甚明显,呈较窄过渡特征.7020GT6铝合金搅拌摩擦焊接头后退侧热机影响区的典型形貌见图3d),其再结晶特征可参考前进侧的.热影响区只受到热的作用,不发生晶粒变形.根据焊接工艺的不同,有时候晶粒会有所长大,部分晶粒内部因回复而形成了细小的亚晶粒;有时候晶粒大小无变化,晶粒内部也无明显亚晶存在,其晶粒特征与母材的并无明显不同.7020GT6铝合金搅拌摩擦焊接头热影响区的典型形貌见图3e),可见晶粒无变形,部分晶粒内部可观察到亚晶.
2.3 各区域微观组织中第二相的表征分析
6061GT6铝合金母材显微组织为α(Al)+块状未溶或难溶相+弥散第二相 Mg2Si,见图4a).颗粒较大的块状未溶相或难溶相,对材料的强度不起明显作用,而弥散第二相 Mg2Si是主要强化相.焊核区在力和热的作用下,块状未溶或难溶相被破碎成较小颗粒状;弥散第二相发生溶解,在后续冷却过程中又再次析出,发生了“重固溶”[4].6061GT6铝合金搅拌摩擦焊接头焊核区典型的显微组织
形貌见图4b),为α(Al)+破碎的较小未溶或难溶相+重固溶后析出的弥散第二相.热机影响区受到力和热的作用较焊核区的要小,只有部分未溶或难溶相被破碎成细小颗粒,也只有部分弥散第二相发生了“重固溶”.6061GT6铝合金搅拌摩擦焊接头前进侧热机影响区典型的显微组织形貌见图4c),为α(Al)+部分原始块状未溶或难溶相+部分破碎的较小未溶或难溶相+弥散第二相(包括原始弥散第二相和重固溶后析出的弥散第二相),焊核与前进侧热机影响区界限明显.6061GT6铝合金搅拌摩擦焊接头后退侧热机影响区典型的显微组织形貌见图4d),即使减小放大倍数,焊核与热机影响区间的界限也不甚明显,第二相特征参考前进侧的.热影响区仅受到热的作用,块状未溶或难溶相未发生任何变化,弥散第二相有些发生了聚集长大,即发生了“过时效”[4],导致材料软化.6061GT6铝合金搅拌摩擦焊接头热影响区典型的显微组织形貌见图4e),为α(Al)+原始块状未溶或难溶相+弥散第二相(包括原始弥散第二相和过时效长大的弥散第二相).
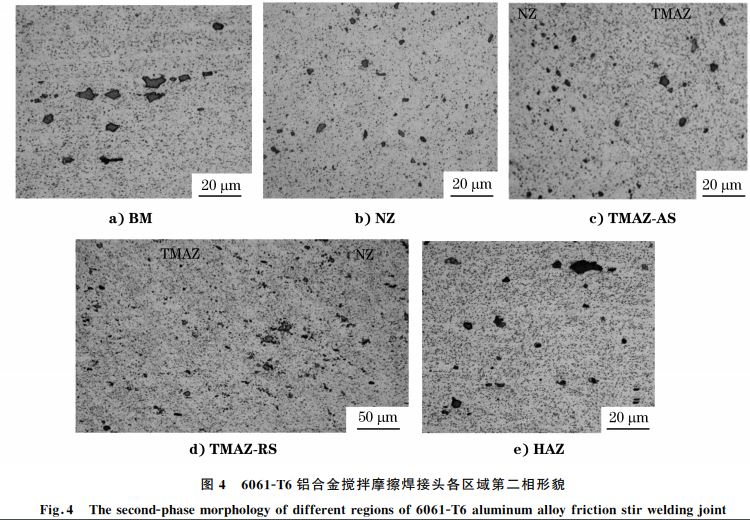
3 焊接接头缺陷的金相表征
3.1 洋葱环
洋葱环是在焊核部位形成的形如洋葱截面的环状结构,其低倍形貌见图5a).洋葱环的实质是搅拌针旋转前进时,带动的软化层与上一软化层之间
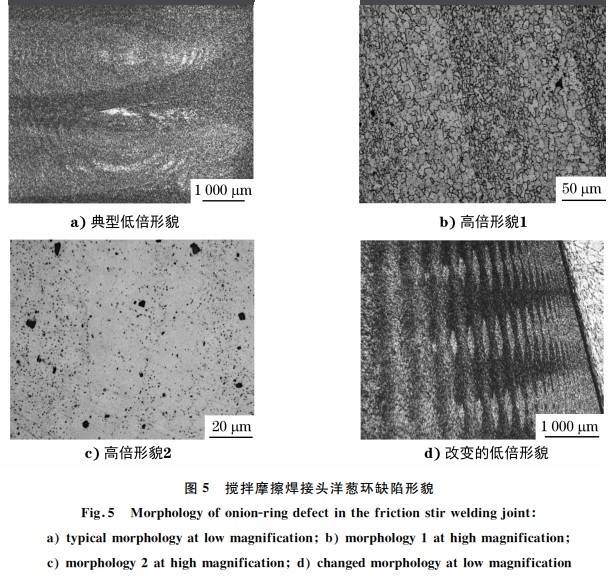
相对移动、摩擦、叠加而产生的一种轨迹[5].其危害是为裂纹的扩展提供了便利通道,同时也会降低材料的断裂韧性[6].
洋葱环在大部分试样中清晰可见,而且在前进侧比后退侧更明显,低倍下的环状结构在高倍下的特征如下:有些是再结晶晶粒大小不等交替形成的,典型形貌见图5b);有些是弥散相质点析出数量不同交替形成的,典型形貌见图5c).由于工艺和材料的不同,洋葱环会在典型形貌基础上发生一些改变,有些洋葱环沿焊核纵向发散,呈平行特征,见图5d).
3.2 Z型线缺陷
Z型线缺陷是由焊接工艺与搅拌工具的特征所决定的,原始界面上的氧化膜或杂质等只能分散到焊缝金属中,当搅拌工具焊接速度和旋转速度不合适时,氧化膜破碎分散不充分,将弥散分布成 Z 型或S型的线缺陷,产生一种结合强度低、局部性能不均匀的线状缺陷.这种搅拌摩擦焊接工艺固有的缺陷虽然对接头的静载强度影响很小,但会对焊接接头的疲劳行为产生较大影响[7].另外它对焊态接头的力学性能影响不大,但会明显降低经过热处理接头的力学性能,因为热处理后会在 Z型线缺陷附近产生微裂纹[7].X射线探伤无法检测到该类缺陷,但通过金相侵蚀后能清晰地观察到该类缺陷[8],其典型形貌见图6a);放大后呈氧化物颗粒聚集特征,见图6b);其对应的抛光态形貌则非常浅显,弥散氧化物颗粒呈聚集特征,见图6c).抛光态氧化物颗粒经过金相侵蚀后颗粒边界被蚀刻,颜色加深,所以金相侵蚀后更容易识别.
3.3 吻接缺陷和钩状缺陷
吻接缺陷(即未焊合缺陷)是在对接焊中,在对接缝的最底部由于焊接热量较弱或者由于搅拌针长度稍短而形成的一种假性连接.这种连接是逐步过渡的,从完全的对接缝到类似于热机影响区的半塑性化假性连接直至完全是焊核程度的塑性化连接.研究表明,半塑性化程度的假性连接对接头的塑性和强度影响不明显[9].这种缺陷只有通过金相侵蚀才能明显呈现,其典型形貌见图7a).图7a)中不存在完全的对接缝,完全对接缝是由原始晶粒组成的;类似于热机影响区的半塑性化假性连接部位由部分再结晶组织与部分弯曲变形长晶粒组织组成;焊核程度的塑性化连接部位由两侧已经完全发生再结晶的组织组成.
钩状缺陷是在搭接焊中,接头中搭接的上下板边界线横缝向焊缝内部扩展的一种弯曲缺陷.它与吻接缺陷性质一样,也是逐步过渡的,从完全的搭接横缝到类似于热机影响区的半塑性化假性连接直至完全是焊核程度的塑性化连接,其典型形貌见图7b).
3.4 孔洞缺陷
孔洞的形成主要是由于焊接过程中热输入量不够,达到塑性化状态的材料不足,材料流动不充分而导致在焊缝内部形成材料未完全闭合的现象.当采用不带螺纹的柱状或锥状搅拌针的搅拌头进行焊接时,所得接头容易出现该类缺陷.典型的孔洞缺陷低倍形貌见图8,可以观察到多个孔洞缺陷。
3.5 隧道型缺陷
隧道型缺陷或者是由焊速太快引起的,焊速过快导致局部热输入量降低,使得焊核塑性化程度降低而导致隧道型缺陷的产生;或者是由于转速过高,塑性材料填充搅拌针行走形成空腔的能力变弱,焊缝内容易形成一条狭长而且平行于焊接方向的隧道沟.总之焊速、转速都很高时,接头内部容易出现贯穿前后的巨大隧道型缺陷[10G11].隧道型缺陷也可以说是孔洞缺陷沿焊接方向一直延伸而形成的.图9a)中隧道型缺陷发生在轴肩搅拌区与搅拌针搅拌区的交界处,放大后形貌见图9b),可见隧道型缺陷周围伴生被搅拌断裂开的原始大晶粒,晶粒破碎不完全且未发生再结晶,进一步说明该处能量较低,塑性化程度较弱,以致形成隧道型缺陷。
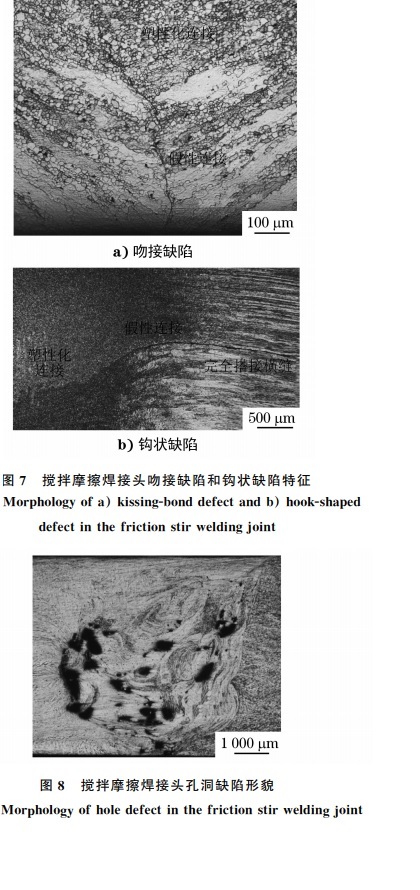
4 结论
(1)铝合金搅拌摩擦焊焊接接头低倍形貌主要有上宽下窄的河床型、上下宽度相近的鼓型以及上尖下圆的壶嘴型3种类型.一般焊速低时,易形成河床型;转速增加,形成上下宽度相近的鼓型;壶嘴型是轴肩搅拌区和搅拌针搅拌区这两个区域差别比较明显时形成的.
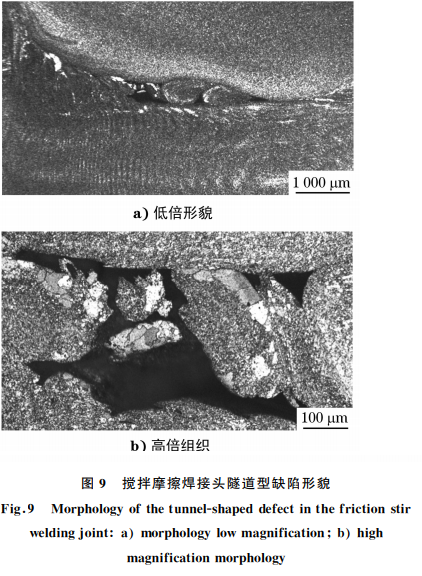
(2)铝合金搅拌摩擦焊接头主要分为焊核区(NZ)、热机影响区(TMAZ)、热影响区(HAZ)和母材(BM)4大区域.在焊核区又可细分为上部轴肩搅拌区和下部搅拌针搅拌区.热机影响区从不同方向上可以分为前进侧热机影响区和后退侧热机影响区,以及轴肩搅拌区的热机影响区和搅拌针搅拌区的热机影响区。
(3)7020G6铝合金各区域的再结晶特征为:母材晶粒呈轧制的拉长粗晶粒;焊核主要为细小等轴再结晶晶粒;热机影响区为原始粗晶粒弯曲变形,部分晶界上可观察到细小再结晶晶粒,部分大晶粒内部可观察到亚晶;热影响区晶粒无变形,部分晶粒内部可观察到亚晶。
(4)6061G6铝合金各区域的第二相分布特征如下:母材为α(Al)+块状未溶或难溶相+弥散第二相 Mg2Si;焊核区为α(Al)+破碎的较小未溶或难溶相+重固溶后析出的弥散第二相;热机影响区为α(Al)+部分原始块状未溶或难溶相+部分破碎的较小未溶或难溶相+弥散第二相(包括原始弥散第二相和重固溶后析出的弥散第二相);热影响区为α(Al)+原始块状未溶或难溶相 + 弥散第二相(包括原始弥散第二相和过时效长大的弥散第二相)。
(5)洋葱环是在焊核部位形成的形如洋葱截面的环状结构,其实质有些是再结晶晶粒大小不等交替形成的,有些是弥散相质点析出数量不同交替形成的。
(6)Z型线缺陷是原始界面上氧化膜破碎分散不充分,弥散分布成 Z型或 S型的线缺陷.金相侵蚀后氧化物颗粒边界被蚀刻,颜色加深,所以金相侵蚀的方法能清晰地观察到该类缺陷。
(7)吻接缺陷和钩状缺陷性质一样,是在对接或搭接焊中,在对接缝或搭接缝处形成的一种假性连接,这种连接是逐步过渡的,从完全的对接或搭接缝到类似于热机影响区的半塑性化假性连接直至完全是焊核程度的塑性化连接。
(8)孔洞缺陷是焊缝内部形成的一种材料未完全闭合的现象,隧道型缺陷是孔洞缺陷沿焊接方向一直延伸而形成的.它们主要是由于焊接过程中热输入量不够,塑性化程度不足,材料流动不充分而导致的。